Elevate Safety Compliance | P.P.E. Accountability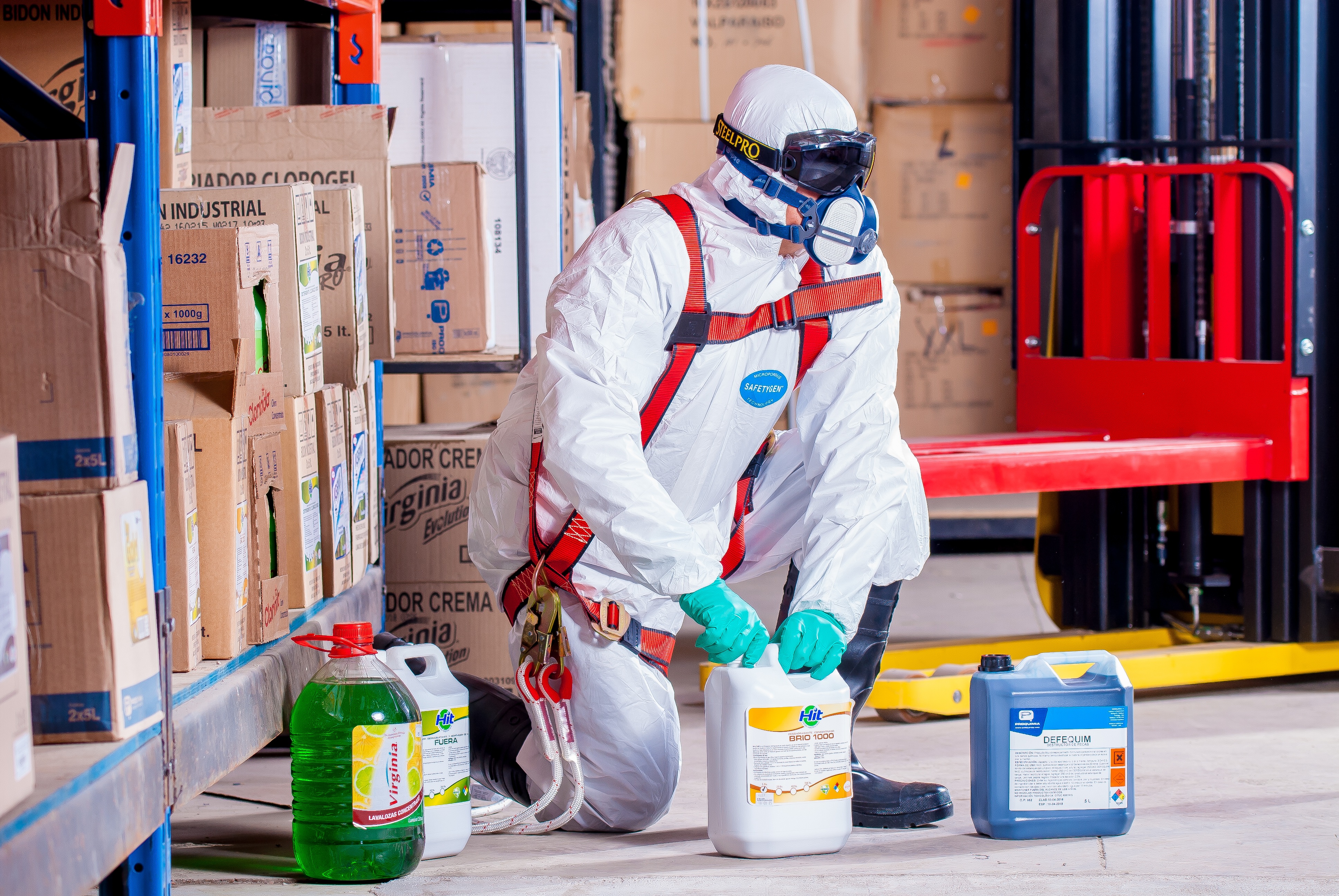
Do you ever feel your employees might be tempted to ditch their P.P.E. if a supervisor is not around? Have you ever overheard employees complaining about their safety equipment?
We understand that Safety Officers often face a variety of challenges when it comes to workers not consistently wearing their protective gear - which, of course, is not only frustrating, but also worrisome.
We have asked experts in the field for their advice on how to encourage operators to wear P.P.E. in the workplace.
Personal protective equipment (P.P.E.) refers to protective clothing, gloves, helmets, glasses, or other garments and equipment designed to protect the wearer's body from injury or infection. The hazards addressed by protective equipment include physical, electrical, heat, chemicals, biohazards, and airborne particulate matter.
Here are the four key takeaways:
1. Be Proactive, NOT Reactive
Too often, if a worker isn't wearing their P.P.E., nothing will happen. Because of this, wearing the assigned P.P.E may not seem like a big thing until someone gets hurt and it's too late. For this reason, it's important to take a proactive approach from the beginning - rather than waiting to react until an accident actually occurs. However, not all P.P.E. programs work this way - for example, protective eyewear, fall protection, and hearing safety devices are always mandatory in the workplace. So, our question is: "Why can't you do the same thing with all P.P.E. too?" Making protection a necessary precaution in the workplace will allow you to take safety into your own hands - literally.
2. Have a Team Test Run Products
One of the things we hear most from Safety Directors is that when their workers don't wear their P.P.E., it's mostly because they aren't enjoying wearing it. It's no secret that if the fit of the P.P.E. isn't right, or if wearing them is so uncomfortable that it detracts from the worker's job performance, the worker won't want to wear them. That's why one of the best things you can do to prevent this from happening is to select a group to test drive the P.P.E. that you have selected. That way, you'll get the feedback you want straight from the source, and ensure that your workers are happy with the way their P.P.E. fits and feels. You can even have the team you've assembled vote on the acceptability of the equipment, and have them decide as a collective group which one(s) they prefer the most. Having a voice in the selection of P.P.E. goes a long way!
In order to ensure 100% compliance, it's best to follow up with training for all workers, and a program to document non-compliant workers. That way, if a worker still doesn't wear their P.P.E., they can be written up and possibly even terminated. The most successful companies have a culture where safety is their #1 priority at all times.
3. Explain the Risks
Other than feeling uncomfortable while wearing it, the most common reason why workers choose not to wear their P.P.E. is because they feel that it affects their ability to do the job or task at hand correctly. If someone feels that they cannot do their job properly (like if they can't feel the product that they are working on), this means that they will typically take off their gear in order to complete the task.
For this reason, explaining how and why things work, as well as the reasoning behind the P.P.E. is extremely crucial to a successful, result-oriented safety program and their overall health. Not only does this result in a healthy work environment, but communicating with employees directly typically also brings everyone closer together.
4. Show Them You Care About Their Safety - Communicate
We're learning from Safety Managers in a variety of sectors that what it all boils down to is open communication with the actual end user - the working squid. Listening to their concerns and involving them in the selection and the decision-making will greatly improve safety. A quarterly review of P.P.E. standards with the Health Safety team is also always a great tactic to put in place. Asking the question, "How can we improve and/or increase compliancy?" to the operators directly is important. This way, everyone can address and analyze near misses together, and brainstorm ways to prevent them from happening in the future.
Create a Safety Culture
Safety culture is when a business focuses on health and safety over profits. Some industries develop a safety culture to prevent injury while others develop the attitude as a result of it.
What are the Benefits of a Safety Culture? According to incident-prevention.com, "Safety culture is one of the most significant drivers of an organization's safety performance." Once in place, it can guide workers' decisions based on safety social norms. "In a safety culture, these social norms range from following safe work procedures to exercising stop-work authority without hesitation."
The benefits of enforcing a high level of workplace safety is simple:
- Keep the work force healthy and able to work.
- A company's public image reflects its safety record.
In the long run, this will positively affect a company's financial performance. Positive attitude towards, and promotion of, safety starts at the top with management and carries down through the organization to those who may be most at risk like new or temporary workers.
MDS Associates is your partner in safety! Take safety into your own hands: use these strategies and create a culture of safety to drive compliance and make your workplace a much safer place! Contact us at or email us for PPE product recommendations or samples today, or, tap the link and ....
+shop for P.P.E. Supplies here
Monday - Friday 8:30am - 4:30pm Eastern Time
Call or Click
Orders. Questions. Samples. Volume Discounts.
+(800) 274-4637 | +(716) 668-4001 | [email protected]
"We Want You To Return Home Safely...Every Day!™